It helps concrete industries to coordinate better and respond faster to their orders. Unlike all other systems in the market, Betolink® GPMATIS 2 continuously updates the dispatcher’s daily schedule for the critical phases of each delivery without the need of digital map monitoring. Furthermore, among its unique advantages are the ability to manage the additives used on site as well as the samples (cubes) taken by the driver.
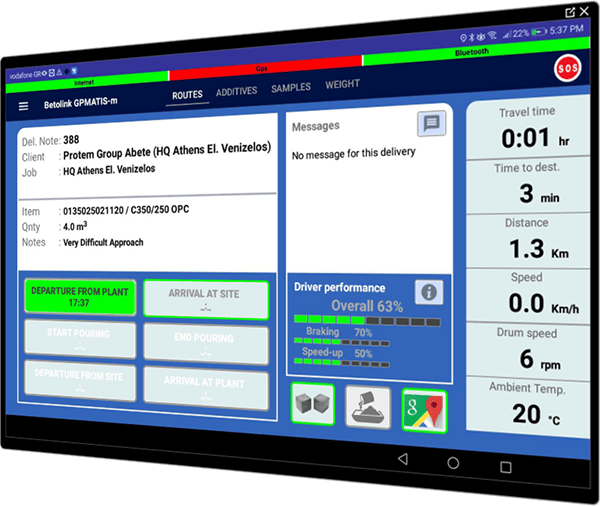
Betolink® GPMATIS 2
Fleet tracking through Betolink® GPMATIS 2 has a completely different philosophy from that of almost all the other generic fleet monitoring systems. It is not an independent system that is limited to displaying and logging the position of each vehicle on a digital map that the dispatcher has to keep an eye on in order to extract meaningful conclusions (that is inefficient in practice).
The purpose of our system is to process the data received by the vehicles and provide all the critical information that helps a dispatcher to improve coordination and speed up the execution of the daily orders. It is a dedicated system designed for ready mixed companies, acting as a real assistance tool even for unexperienced dispatchers.
Fleet tracking through Betolink® GPMATIS 2 has a completely different philosophy from that of almost all the other generic fleet monitoring systems. It is not an independent system that is limited to displaying and logging the position of each vehicle on a digital map that the dispatcher has to keep an eye on in order to extract meaningful conclusions (that is inefficient in practice).
The purpose of our system is to process the data received by the vehicles and provide all the critical information that helps a dispatcher to improve coordination and speed up the execution of the daily orders. It is a dedicated system designed for ready mixed companies, acting as a real assistance tool even for unexperienced dispatchers.
CAPABILITIES – ADVANTAGES
- Real-time bidirectional communication with the Production Management, Dispatching and Ticketing software Betolink® Pro.
- Zero additional labor costs for supervising the system.
- Reduce the operating costs of the company due to optimization of its transportation, fuel costs and rejection errors.
- Eliminate errors in deliveries of concrete to the projects and increase overall security level of the company.
- The customer service level is increased. The feeding history of each customer/project is recorded automatically, thus providing you with a reliable service report.
- Significantly reduced cost of acquiring and installing required hardware in vehicles.
- System’s updates and upgrades can be automatically downloaded to the vehicles equipment.
- Once the appropriate equipment is installed in the vehicles, the chemical additives used in projects and water (if it is allowed), are automatically dosed and their quantities are recorded.
- Ability to interface with the Betolink® Laboratory software for taking concrete cubes (samples) by the drivers on the site.
- Driver’s behavior can be also monitored by using the optional software “GPMATIS 2 Driver Assistance”.
DETAILED PRESENTATION
Each vehicle must be equipped with a common tablet on which our android application is installed. The tablet communicates with the dispatching center and the corresponding Betolink® Pro software via 3G-4G network (a SIM card is necessary). The vehicle may optionally be equipped with a controller that communicates wirelessly with the Tablet.
The controller, depending on the customer’s choices, is connected to additional sensors that must be installed on the vehicle and can detect: a) mixer’s drum rotation speed and direction b) ambient and concrete temperature c) the quantity of additives the driver unloads at the site.
- As soon as a vehicle is loaded and the delivery ticket is printed, detailed information regarding the specific delivery appear on the Tablet’s screen. Drivers can have both visual and voice navigation assistance.
- During transit, the Tablet sends the GPS location and speed data to the system. The communication rate is defined parametrically so that the data volume is optimized according to the customer’s needs. In this way, the data usage charges are controllable.
- After arriving at the site, the driver can manually register the unloading start and end time by pressing the relevant buttons on the screen. This process can be recorded automatically by installing our optional controller and sensors on the vehicles.
- The system displays all of the above data on Betolink® Pro daily program in a manner that is both ergonomic and legible. The dispatcher and the plant operator are instantly aware of the following data , without having to keep an eye on maps:
- Vehicles heading to sites and their estimated time of arrival.
- Vehicles present at sites whether they are unloading or they are on hold.
- Actual concrete volume delivered per site, the volume on hold and the volume on the way to the site – in other words, the actual delivery rate per site.
- Vehicles returning to the plant and their estimated time of arrival.
- Available vehicles (those that are idle at the plant)
- On-line Statistics for each project based on the historical data of previous routes. - Display of every vehicle’s location on Google Maps, similar to what is offered by generic systems. This feature is used mainly for guiding vehicles that have difficulties in reaching their destination or in case of an alarm when the exact geographic location of the vehicle is needed. However our system also has the following advantages:
- It is possible to only display and observe the vehicles which are used for a specific project on the digital maps. This way the dispatcher receives targeted information on the geographical area of a single project by temporary disabling the display of all other vehicles on the map.
- Each route can be traced after its completion. By selecting a vehicle and a corresponding delivery note number, the exact route it made can be tracked back on the map as well as the locations where possible alarms went off during this route. - Except the above, PROTEM’s fleet tracking system is not limited to these functions. It also features automatic alarms for the following cases:
- Unwanted stops in case a vehicle exceed a predefined waiting time according to the local area’s traffic conditions.
- Speed limit exceedance, which is parametrically set for each vehicle.
- Reaching to a site other than the one ordered or unloading in forbidden places (sabotage).
- Maximum allowed concrete transportation time exceeded (e.g. 90 minute rule).
- Site’s feeding rate lower than the one required.
- Emergency situation for the Driver (when a driver presses the panic button) - Automatic doses and records the quantities of the chemical additives and water (if it is allowed) that can be used in projects. Mostly the additives on site are being managed by the drivers but in well-organized companies with a strict quality policy, the permission to add additives on site should be centrally given by the dispatcher. Our system support both scenarios.
- Automatic concrete temperature measurement during unloading. Additionally, a second temperature can be taken by the driver using a portable temperature probe which he places himself inside the concrete sample that he takes at site. Concrete temperature measurement can be registered in our system by the driver even manually in case he uses simple hand thermometers which cannot be connected to our system.
- Drivers can register on their tablet also the cubes they take on site. This information is automatically downloaded to the laboratory department (Betolink® Laboratory software), eliminating the risk of lost cubes and the labor cost for duplicates entries.
APPLICATION AND OPERATION
No additional work is required both for both the dispatcher and the drivers on order to operate the Betolink® GPMATIS 2 system. Since the company is already using the Betolink® Pro software for its daily production scheduling and execution, then no further action is required for tracking its fleet. The benefits for the dispatchers are obvious on system’s detailed description. On the contrary, drivers will be benefited from using the tablet because of the digital navigation assistance they will automatically get for each order. It is also no longer required to fill in the delivery notes about the time of arrival, unloading and return to plant with handwriting.
The Accounting department is also facilitated because of the elimination of many double entries and crosschecks. Routes data is automatically saved into the digital records of the already issued Delivery Notes and any extra charges provided by the contract are calculated and notified to the invoicing department.
Last but not least the Quality Control Laboratory’s tasks are facilitated since the drivers can register the samples taken on the project. All the information automatically updates the Betolink® Laboratory software without double-registrations, thus nullifying the danger of omitting or mistaking certain data.
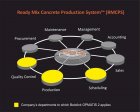
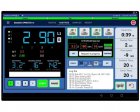
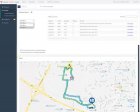
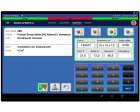
Open to new challenges
Do you have any idea of cooperation, you believe that our know-how can be adapted to your own field?
Do you have a special project and are looking for suitable partners to implement it? We are open to new opportunities...
Connect with us
Do you prefer live communication? So do we!
We'd love to speak with you.
Contact us
Get support
Do you have any technical questions?
Our experienced engineers will gladly discuss with you.
Technical Support
Stay updated
Are you interested in receiving updates
about our new products and offers?
Subscribe
Protem Group S.A.
3, 35th Str., 133 41 Industrial Park
Ano Liossia / Athens, Greece
info@protem.gr
Τ. +30 210 5716500
F. +30 210 5710008
GCR No: 7633901000
The Company
Contact
Company News
Legal Information
1989 - 2024
Φέτος έχουμε γενέθλια! Τον Ιούλιο κλείνουμε τα 35!
35 χρόνια σκληρή δουλειά με αγάπη, αφοσίωση και με σημαντικές επιτυχίες! 35 δημιουργικά χρόνια. Θα τα γιορτάζουμε μαζί σας μέχρι το τέλος του έτους με πλούσια δώρα, πολλές προσφορές, και φυσικά, νέα προϊόντα.
Μείνετε συντονισμένοι στην ιστοσελίδα μας για να μαθαίνετε πρώτοι τις προσφορές μας και ακολουθήστε μας στο Facebook για να πάρετε μέρος σε διαγωνισμούς με πλούσια δώρα Protem!
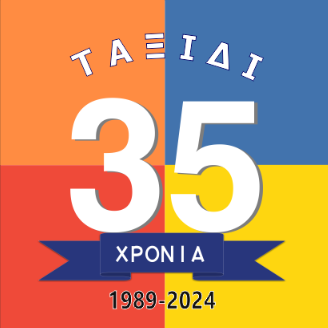
ΟΙ ΑΠΟΣΚΕΥΕΣ ΜΑΣ
Ηθική, Ακεραιότητα και Διαχρονικές Αξίες
Δείτε μια σύντομη ιστορική αναδρομή με τους σημαντικούς σταθμούς της τριακονταπενταετούς διαδρομής μας
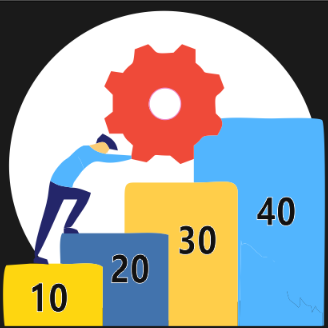
ΤΟ ΜΥΣΤΙΚΟ ΜΑΣ
Μεθοδική Δουλειά, Ομαδικότητα και πολλή Υπομονή
Μαθαίνουμε από τα λάθη μας αλλά περισσότερο, μαθαίνουμε από τις επιτυχίες μας.

Η ΔΙΑΦΟΡΕΤΙΚΟΤΗΤΑ ΜΑΣ
Πάθος για Καινοτομία
Ο εύκολος δρόμος της αντιγραφής και της μίμησης μάς είναι άγνωστος. Αναπτύξαμε σταδιακά τη δική μας τεχνογνωσία, που την εμπλουτίζουμε διαρκώς με νέες ιδέες και τεχνολογίες. Είμασταν και παραμένουμε ανοιχτοί σε νέες προκλήσεις.
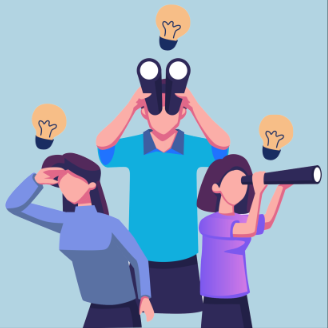
ΟΙ ΟΛΙΣΤΙΚΕΣ ΜΑΣ ΛΥΣΕΙΣ
Εσείς Ακόμη Ψάχνετε πώς να Υλοποιήσετε τις Ιδέες σας;
Ο όμιλος PROTEM είναι 3 εταιρείες σε 1. Με τα 3 τμήματά μας, ηλεκτρονικών – μηχανολογικών – λογισμικών, σχεδιάζουμε, κατασκευάζουμε, εγκαθιστούμε και υποστηρίζουμε λύσεις από το Α έως το Ω για τη Βιομηχανία Σκυροδέματος.
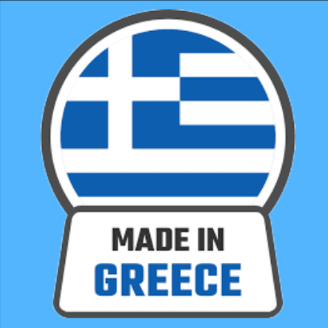
Η ΠΕΡΗΦΑΝΙΑ ΜΑΣ
Επιμένουμε Ελληνικά
Παρά τα εμπόδια και τις τρικλοποδιές του κράτους που πρέπει διαχρονικά να ξεπερνάμε, όλοι οι ευσυνείδητοι και νομοταγείς επιχειρηματίες στη χώρα μας, ακόμη περισσότερο δε οι κατασκευαστές, η PROTEM επιμένει Ελληνικά.
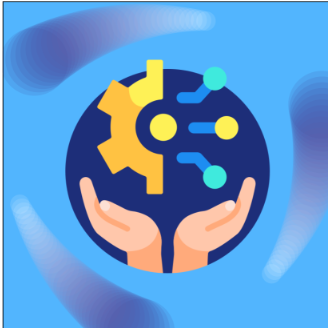
ΟΙ ΣΤΟΧΟΙ ΜΑΣ
Με το βλέμμα στραμμένο στο μέλλον
Η Protem στοχεύει πάντοτε σε ένα καλύτερο και πιο ελπιδοφόρο μέλλον. Η δύναμή μας ήταν και παραμένει το άρτια εκπαιδευμένο ανθρώπινο δυναμικό μας. Η διαρκής ενσωμάτωση νέων επιστημόνων στην κοινότητα, με τις ίδιες αρχές και τη φιλοσοφία της εταιρείας, εγγυώνται μια επιχειρησιακή συνέχεια αντάξια του παρελθόντος.